Manufacturing Industries
- Classification of Industries:
- Based on raw material:
- According to their main roles:
- Based on Ownership:
- Major Industries:
- Iron and Steel Industry:
- Government Schemes for the Iron and Steel Industry:
- Cotton Industry / Technical Textiles:
- The Apparel Sector
- Jute Industry
- Government Initiatives for the Promotion of Jute:
- Sugar Industry:
- Petrochemical Industry:
- Polymers:
- Synthetic fibres:
- Liberalisation, Privatisation and Globalisation:
- Industrial Regions in India:
- Mumbai-Pune Industrial region:
- Hugli Industrial Region:
- Bangalore-Chennai Industrial Region:
- Gujarat Industrial Region:
- Chotanagpur Region:
- Vishakhapatnam-Guntur Region:
- Gurgaon-Delhi-Meerut Region:
- Kollam-Tiruvanantapuram Region:
- Related FAQs of Manufacturing Industries
- Much lower than 25-35% in some East Asian Economies.
- The growth rate is around 7% per annum. The desired growth rate over the next decade is 12%.
- Industrial Location: These are influenced by the availability of raw materials, labour, capital, electrical power, and the market.
- Many industries sometimes ten to come together to make use of advantages offered by the urban centres known as agglomeration economies.
Classification of Industries:
Based on raw material:
- Agro Based: cotton, woollen, jute, silk, textile, rubber and sugar, tea, coffee, edible oil.
- Mineral Based: Iron and steel, cement, aluminium, machine tools, petrochemicals.
According to their main roles:
- Basic or Key industries: supply raw materials for manufacturing units. For example, Iron and steel, copper smelting, and aluminium smelting.
- Consumer industries: Produce goods for direct use by consumers – Sugar, tootHimachal Pradeshaste, paper, sewing machines, fans etc.
Based on Ownership:
- Public sector: Owned and Operated by govt. agencies
- Private sector: Owned and operated by individuals or groups of individuals.
- Joint Sector: Run by the State and individuals or a group of individuals; For example, OIL (Oil India Ltd.) is jointly owned by the public and private sectors.
- Cooperative sector: Owned and operated by Producers and suppliers of raw materials. They pool the resources and share profits or losses proportionately; For example, the Sugar industry in Maha and the coir industry in Kerala.
Major Industries:
Iron and Steel Industry:
Raw Material: For the production of 1 Tonne of Iron – 1.5 tons of Iron ore, 1.4 tons of coal, 0.3 tons of limestone, 0.1 tons of manganese and 0.1 tons of dolomite is required. Further, high-quality coal is required in the Blast Furnace. It can either be Anthracite or the coal is first converted to coke to enhance its quality.
Location:
- All these raw materials are gross (weight losing), therefore, the best location for the iron and steel plants is near the source of raw materials.
- The industry is also located near the exporting units. For example, the Vizag steel plant.
- Import of Anthracite.: Location at the port.
India includes large steel plants as well as mini steel mills. The industry also includes secondary producers: rolling mills and Ancillary Industries.
There is a crescent-shaped region comprising parts of Chhattisgarh, Northern Orissa, Jharkhand and western West Bengal, which is extremely rich in high-grade iron ore, good quality coking coal and other supplementing raw materials.
India’s total steel Production:
India produced 140 Million tonnes of steel in 2023 (v/s 1020 MT of China). For the past several years China has produced approximately 6 times the steel that India has produced.
Despite being the world’s 2nd largest producer of steel, India’s annual per capita steel consumption is 74.1 kg and is 1/3rd the global average (224.5kg).
In recent times, the consumption of steel in China has stagnated, which has forced it to export steel to the world. Currently, it is the largest producer, and consumer as well as the exporter of steel.
Integrated Steel Plants in India:
Presently, there are 10 primary integrated and many mini steel plants in India. Out of these, TISCO, IISCO, and VISL were established before Indian Independence.
- TISCO: very close to the Mumbai-Kolkata railway line and about 240 km away from Kolkata, which is the nearest port for the export of steel.
- Water from rivers Subarnarekha and Kharkai; Also, Koel river nearby.
- Iron ore: Noamundi and Badam Pahar and
- Coal: From Joda mines in Orissa. Coking coal comes from the Jharia and west Bokaro coalfields.
- IISCO: Indian Iron and Steel Company: first factory at Hirapur and later on another at Kulti. In 1937, the Steel corporation of Bengal was constituted in association with IISCO and set up another iron and steel-producing unit at Burnpur (West Bengal).
- Location: All 3 plants under IISCO – are located very close to Damodar valley coal fields (Raniganj, Jharia, and Ramgarh). Iron ore comes from Singhbhum in Jharkhand. On the Kolkata-Asansol railway line.
- Water: from the Barakar River, a tributary of the Damodar.
- Steel production from IISCO fell considerably in 1972-73 and the plants were taken over by the government.
- VISL: Visvesvaraiya Iron and Steel Works: initially called Mysore Iron and Steel Works;
- Location: Near Kemangundi (iron ore) in the Bababudan hills. East of Mangaluru.
- Raw Material:
- Limestone and manganese are also locally available.
- Coal: Till 1951, Charcoal was obtained by burning nearby forests. Afterwards, electric furnaces were installed using hydroelectricity from the Jog Falls hydel project.
- Water: Bhardravati river.
- Produces specialised steels and Alloys.
Steel Plants Established Post-Independence
After Independence 3 more plants (during the 2nd Five-year plan) were set up with foreign collaborations: Rourkela in Odisha, Bhilai in Chhattisgarh and Durgapur in WB. These were Public sector plans under HSL (Hindustan Steel Limited);
In 1973, SAIL (Steel authority of India Ltd) was created to manage these.
- Rourkela Steel Plant – 1959: Sundargarh (Odisha) in collaboration with Germany.
- Raw material: Proximity: Coal-Jharia (Jharkhand), Iron-Sundargarh and Kendujhar.
- Power: Hirakund – electric furnaces and
- Water: Koel and Sankh Rivers
- Bhilai Steel Plant – 1959: Russian collaboration: Durg Distt of Chhattisgarh. ON Kolkata-Mumbai rail route. The bulk of steel goes to Hindustan Shipyard at VishakhapaTamil Naduam.
- Iron: Dalli-Rajhara mine
- Coal: Kobra and Kargali coal fields.
- Water: Tanduladam
- Power: Korba Thermal power station.
- Durgapur Steel Plant – 1962: UK collaboration. In Raniganj and Jharia coal belt. On Kolkata-Delhi Railway route.
- Iron ore from Noamundi.
- Power and water: Damodar Valley Corporation (DVC).
- Bokaro Steel Plant – 1964 Russian collaboration. On the principle of transportation cost minimisation by creating Bokaro-Rourkela combine. It receives iron ore from the Rourkela region and the wagons in return take coal to Rourkela.
- Other Raw material: within a radius of 350km.
- Water and Hydel power: Damodar Valley Corporation (DVC).
Other Steel Plants: Away from raw material sources – 4th plan period.
- Vizag Steel Plant: first port-based plant, Operation in 1992.
- Vijaynagar Steel Plant in Hospet – Karnataka.
- Salem Steel Plant in Tamil Nadu was commissioned in 1982.
All public sector undertakings produce steel through SAIL while TISCO though Tata Steel.
Challenges in the Steel Sector
We are not able to perform to our full potential, largely due to:
- High cost and limited availability of coking coal. This results in import dependency on coal.
- Lower productivity of labour
- Irregular supply of energy
- Poor transportation and logistics infrastructure.
- In-efficient steel plants.
- Steel dumping at a lower cost in the world market by China makes Indian steel uncompetitive. Those steel plants that are export-oriented are adversely affected by this. This has led to major bankruptcies in the steel sector in the past.
- Protectionism: countries like the US have started levying import duties to protect themselves from Chinese dumping, which in turn affects even Indian companies.
Government Schemes for the Iron and Steel Industry:
Policy for preferring domestic steel
Policy for providing preference to domestically manufactured Iron and Steel products (DMIandSP) in Government procurement. Through this, Steel imports worth more than Rs. 20,000 cr. have so far been avoided.
‘Ispat India’ Campaign:
It has the following aims:
- Promote appropriate steel usage in the country; i.e. manufacturing of alloys according to needs.
- Leveraging the usage of steel as an easy-to-use, environment-friendly, cost-effective, affordable and strength-giving material.
- Working to ensure raw material security for the sector such as by diversifying our sources of coking coal imports.
Steel scrap policy
- It provides a framework to facilitate and promote the establishment of metal scrapping centres in India for scientific processing and recycling of ferrous scrap generated from various sources and a variety of products.
- It provides standard guidelines for collection, dismantling and shredding activities in an organized, safe and environmentally sound manner.
Mission Purvodaya:
It aims to build an Integrated Steel Hub in eastern India to improve steel availability, strengthen value chains facilitate regional development with job creation. It will be accompanied by new physical and social infrastructure.
Cotton Industry / Technical Textiles:
Two factors make India such a huge cotton textile-producing area:
- Large Cotton producing area in India
- Skilled labour.
- Large Market – India is a tropical country – Cotton most comfortable fabric.
Location of Cotton Industries:
- Cotton is pure raw material: and does not lose weight. Capital or market may determine the location of the industry. The trend is near the market. After Mumbai and Ahmedabad; Mills spread in the 1920s.
- Southern India: mills were set in Uttar Pradesh at Coimbatore, Madurai and Bangalore.
- Central India: Nagpur, Indore, Solapur and Vadodara became cotton textile centres.
- Kanpur is based on local investment.
- Kolkata due to its port facilities.
- The development of hydroelectricity also favoured the location of the cotton textile mills away from the cotton-producing areas. The rapid development of this industry in Tamil Nadu is the result of the abundant availability of hydel power for the mills.
- Lower labour costs at centres like Ujjain, Bharuch, Agra, Hathras, Coimbatore and Tirunelveli also caused industries to be located away from cotton-producing areas.
History of Cotton mills in India
1st mill in 1854 in Bombay. Later, many cotton mills were opened in various cities of Gujarat and Maharashtra. Here Cotton was brought to Mumbai for Export to England. This was used by these mills.
By 1947, India had 423 cotton Mills. After partition major recession occurred in India as good quality cotton growing areas went to Pakistan.
Nevertheless, by 1998, India had 1728 mills; Out of these 192 were under the Public sector and 151 under the Cooperative sector.
The cotton industry can be divided into 2 sectors:
- The decentralised sector includes both handlooms (including Khadi) and power looms. At present, the power looms on the decentralised sector produce more than 59% and the handloom sector produces about 19% of all cotton cloth produced in the country.
- The organised sector has drastically fallen from 81% in the 1950s to only about 6% in 2000.
Major Cotton Textile Centres of India:
Major Textile producing areas of India include:
- Ahmedabad, Bhiwandi, Solapur, Kolhapur, Nagpur, Indore and Ujjain. (all in cotton-producing areas)
- Tamil Nadu has the largest number of mills and most of them produce yarn rather than cloth. Coimbatore: half of all mills in TAMIL NADU. Other: Chennai, Madurai, Tirunelveli Tuticorin, Thanjavur, Ramanathapram and Salem.
- Karnataka: in the cotton-producing areas in the northeastern part of the state. Davangere, Hubli, Bellary, Mysore and Bangalore are important centres.
- Telangana: in the cotton producing: most of the mills are spinning mills producing yarn. The important centres are Hyderabad, Secunderabad, Warangal and Guntur.
- UP: Kanpur is largest centre; Other centres: Modinagar, Hathras, Saharanpur, Agra and Lucknow.
- West Bengal: located in the Hugli region. Howrah, Serampur, Kolkata and Shyamnagar are the important centres.
Cotton Production in India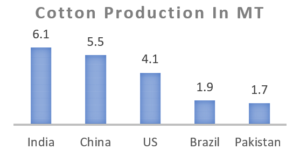
Production of cloth increased by 5 times from 1950-51 to 1999-2000. India is currently the highest producer of Cotton in India. However, it faces stiff competition from manmade or synthetic fibres, exported by China and Japan.
The Apparel Sector
The clothes that are worn are known as Apparel. It includes leatherwear and footwear.
Advantages of promoting the Apparel Sector
- These offer tremendous opportunities for the creation of jobs, especially for women.
- The apparel sector is the most labour-intensive, followed by footwear.
- India has an opportunity to promote because of rising wage levels in China that have resulted in China stabilizing or losing market share in these products.
Challenges faced by the Textile and Apparel sector
It is a no-brainer that the Apparel sector can help India grow tremendously and create a huge number of jobs. However, India faces several stiff challenges in this regard.
- Logistics: The costs and time involved in getting goods from factory to destination are greater than those for other developing countries.India alsoLacks enough warehouses, due to the poor rental economy.
- Labour regulations: ComplexlabourRegulations regarding Mandatory contributions, part-time/contract-based employment and multiple wages acts.
- Rationalisation of taxes: High tariffs on yarn and fibre increase the cost of producing clothing. India imposes 10% tariff on man-made fibres vis-a-vis 6% on cotton fibres.
- Global demand: is shifting from leather footwear towards non-leather footwear due to its physical comfort, aesthetics and price affordability. But India exports mainly leather products. Efforts are required to promote non-leather footwear to effectively capture the market.
- Discrimination in the export market: India faces an 11.4% tariff, whereas:
- Products from countries like Bangladesh enter the EU and the US mostly duty-free since it is categorised as a Least Developed country (LDC).
- Products from countries like VieTamil Naduam attract zero tariffs due to the FTA between the EU and ASEAN.
Jute Industry
The Indian Jute Industry is 2nd largest after Bangladesh. There are more than 110 Jute mills in India, of which 82 are located in West Bengal alone, mostly in the narrow belt of 3km along the 100km bank of Hugli.
The Jute Industry supports 2.61 Lakh workers and 40 Lakh small and marginal farmers who are engaged in the cultivation of jute and mesta.
Factors Affecting the Location of the Jute Industry
- Inexpensive water transport, support of rail, road and waterways to facilitate movement of raw material to mills.
- Abundant water for processing raw jute,
- Cheap labour: The Hugli region gets cheap labour from West Bengal and adjoining states of Bihar, Odisha and Uttar Pradesh.
- Capital: Kolkata, a large urban centre provides banking, insurance and port facilities.
Main Markets for Indian Jute currently: US, Canada, Russia, UAR, UK and Australia.
Challenges faced by the Jute Industry:
- Stiff competition from the international market,
- Synthetic substitute from Bangladesh, Brazil, Philippines, Egypt and Thailand.
- Tumbling internal demand due to unattractive final product.
- Lack of effective Marketing Mechanisms.
Opportunities:
In modern times, new opportunities have arrived for Jute:
- It can be used as a Handicraft Material.
- Environmental Movement: Growing global concerns for environment-friendly, biodegradable materials, have opened the opportunity for jute products. The Government can put a High GST on synthetic materials due to their non-biodegradability and polluting nature.
- It is used in the Construction Industry for curing purposes. It allows water to evaporate slowly to keep the solidifying concrete cool so that no cracks are developed during construction.
Government Initiatives for the Promotion of Jute:
Mandatory Jute packing:
To boost Internal Demand, CCEA has approved that 100% of the foodgrains and 20% of the sugar shall be mandatorily packed in diversified jute bags.
- Jute Packaging Materials Act, 1987: The government is required to provide for compulsory use of jute packaging material in the supply and distribution of certain commodities in the interest of production of raw jute and jute packaging material.
- The Government sector purchases jute bags of more than Rs. 7,500 crore/year for packing foodgrains.
National Jute Policy, 2005:
- Objective: increasing productivity, improving quality, ensuring good prices to jute farmers and enhancing yield per hectare.
Jute ICARE initiative:
Govt. has been supporting close to approximately 2 lakh jute farmers by disseminating improved agronomic practices such as:
- Line sowing using seed drills,
- Weed management by using wheel-hoeing and nail-weeders,
- Distribution of quality certified seeds and
- Providing microbial-assisted retting (the process of separating the fibre from the stem).
These interventions have resulted in enhancing the quality and productivity of raw jute and increasing the income of jute farmers by Rs. 10,000 per hectare.
Other Initiatives
- Jute SMART, an e-govt initiative was launched in December 2016, providing an integrated platform for procurement of B-Twill sacking by Government agencies.
- Use Certified Seeds: Jute Corporation of India has entered into an MoU with National Seeds Corporation for the distribution of 10,000 quintals of certified seeds on a commercial basis.
Sugar Industry:
It is the 2nd most important Agro-based industry in the country. India is the largest producer of both sugarcane and cane sugar and contributes about 8% of the total sugar production in the world. Besides, Khandasari and Gur or jaggery.
Employment:
- More than 4 lakh persons directly and a large number of farmers indirectly. Seasonal industry – because of the seasonality of raw materials.
- Development of the industry on modern lines dates back to 1903 when a sugar mill was started in Bihar. Subsequently, sugar mills were started in other parts of Bihar and Uttar Pradesh
- 1950-51: 139 factories in operation producing 11.34 lakh tonnes of sugar.
- 2000-01: 506 factories and production to 176,99 lakh tonnes.
Location:
It is a Weight-losing crop. The ratio of Sugar to Sugarcane varies between 9-12% depending on a variety of Sucrose content, i.e. from every 100 kg of Sugarcane only 9-12kg of sugar is produced. This influences the location of sugar mills in two ways:
- Sugarcane-producing areas such as UP, Haryana and Punjab are ideal for setting up sugar mills. These are areas with abundant water to produce sugarcane.
- Cold environment: As soon as sugarcane is harvested, its sucrose content starts reducing due to factors such as evaporation. For better recovery, it should crush within 24 hours of harvesting. A cold climate is ideal. For example, Maharashtra and Karnataka.
Major Producers:
- Maharashtra – 1/3rd of total production in India; There are 195 mills in the state, most of which are located in the narrow belt from Manmad in the North to Kohlapur in the South. [East side of Western Ghats]
- UP: 2nd Largest producer of Sugar, even though it holds India’s 50% cane-producing area; More than 150 mills in Uttar Pradesh are concentrated in two belts:
- Doab region: Saharanpur, Muzaffarnagar, Meerut, Ghaziabad, BagHimachal Pradeshat, Bulandshahr District.
- Terai Region: Kheri Lakhimpur, Basti, Gonda, GorakHimachal Pradeshur, and Bahraich are important sugar-producing districts.
Other States:
- Tamil Nadu: Factories are located in Coimbatore, Vellore, Tiruvanamalai, Villupuram and Tiruchchirappalli districts.
- Karnataka: Belgaum, Bellary, Mandya, Shimoga, Bijapur, and Chitradurg districts.
- The industry is distributed in the coastal regions i.e. East Godavari, West Godavari, Vishakhapatnam districts and Nizamabad, and Medak districts of Telangana along with Chittoor district of Rayalseema.
- Bihar: Sarhjhan, Champaran, Muzaffarnagar, Siwan, Darbhanga, and Gaya.
- Punjab: The relative significance has declined, although Gurdaspur, Jalandhar, Sangarur, Patiala and Amritsar are major sugar producers.
- Haryana: sugar factories are located in Yamuna Nagar, Rohtak, Hissar and Faridabad districts.
- Gujarat: comparatively new. Sugar mills are located in the cane-growing tracts of Surat, Junagarh, Rajkot, Amreli, Valsad and Bhavnagar districts.
Petrochemical Industry:
In the 1960s, demand for organic chemicals increased so fast that it became difficult to meet this demand. At that time, the petroleum refining industry expanded rapidly. Many items are derived from crude petroleum, which provides raw materials for many new industries, these are collectively known as petrochemical industries.
Divided into four sub-groups:
- Polymers,
- Synthetic fibres,
- Elastomers, and
- Surfactant intermediate.
India specialises in Polymers and Synthetic fibres
Location
- Raw material: India produces petrochemicals by the means of fractional distillation of Petroleum. The Petrochemicals are its by-products. India imports most of these chemicals and thus, these industries are located close to ports. Mumbai is the hub of the petrochemical industries.
- Cracker units are also located in Auraiya (UP), Jamnagar, Gandhinagar and Hajira (Gujarat), Nagothane, RaTamil Naduagiri (Maharashtra), Haldia (WB) and Vishakhapatnam (AP).
Major government initiatives in the development of Petrochemicals |
Three organisations working petrochemical sector under the administrative control of the Department of Chemicals and Petrochemicals.
One is working on the Production of Polymers: 4.National Organic Chemicals Industries Limited (NOCIL) (private sector), established in 1961, started the first naphtha-based chemical industry in Mumbai. Later, several other companies were formed. The plants located at Mumbai, Barauni, Mettur, Pimpri and Rishra are the major producers of plastic materials. |
Polymers:
Polymers are made from ethylene and propylene – obtained in the process of refining crude oil. Used as raw materials in the plastic industry. Polyethylene is a widely used thermoplastic.
Plastic is first converted into sheets, powder, resin and pellets, and then used in manufacturing plastic products. These are strength, flexibility, water and chemical resistance and low prices.
Production of Polymers
Production of plastic polymers started in India in the late fifties and the early sixties using other organic chemicals.
- About 75% of these units are in the small-scale sector.
- The industry also uses recycled plastics, which constitute about 30% of the total production.
Synthetic fibres:
These are widely used in the manufacturing of fabric due to inherent strength, durability, washability, and resistance to shrinkage. Industries manufacturing nylon and polyester yarns are located in Kota, Pimpri, Mumbai, Modinagar, Pune, Ujjain, Nagpur and Udhna. Acrylic staple fibre is manufactured at Kota and Vadodara.
Liberalisation, Privatisation and Globalisation:
The New Industrial Policy was announced in 1991. Within this policy, measures initiated are:
- Abolition of industrial licensing: abolished except for 6 industries related to security, strategic or environmental concerns. The number of industries reserved for the public sector since 1956 has been reduced from 17 to 4. Industries related to atomic energy, substances specified in the Schedule of the Department of Atomic Energy as well as Railways have remained under the public sector.
- Free entry to foreign technology,
- Foreign investment policy,
- Access to the capital market,
- Open trade,
- Abolition of phased manufacturing programme, and
- Liberalised industrial location programme.
Industrial Regions in India:
Several indices are used to identify the clustering of industries, important among them are:
- Number of industrial units,
- Number of industrial workers,
- Quantum of power used for industrial purposes,
- Total industrial output, and
- Value added by manufacturing, etc.
Mumbai-Pune Industrial region:
From Mumbai-Thane to Pune and adjoining districts of Nashik and Solapur.
Other centres: Kolaba, Ahmednagar, Satara, Sangli and Jalgaon districts, including Kalyan, Thane, Trombay, Pune, Pimpri, Nashik, Manmad, Kolhapur.
The development of this region started with the location of the cotton textile industry in Mumbai. Mumbai, with its cotton hinterland and moist climate, favoured the location of the cotton textile industry.
- Origin: The opening of the Suez Canal in 1869 provided impetus to the growth of Mumbai port. Machineries were imported through this port.
- Hydroelectricity was developed in the Western Ghat region to meet the requirements of this industry.
- Then Chemical industry developed with the opening of the Mumbai High Petroleum field. Besides, engineering goods, petroleum refining, petrochemicals, leather, synthetic and plastic goods, drugs, fertilisers, electrical, shipbuilding, electronics, software, transport equipment and food industries also developed.
Hugli Industrial Region:
Location: Along the Hugli river, extends from Bansberia in the north to Birlanagar in the south for a distance of about 100 km.
Industries also have developed in Mednipur in the west. Kolkata-Haora from the nucleus of this industrial region.
Important industrial centres of this region are Kolkata, Haora, Haldia, Serampur, Rishra, Shibpur, Naihati, Kakinara, Shamnagar, Titagarh, Sodepur, Budge Budge, Birlanagar, Bansberia, Belgurriah, Triveni, Hugli, Belur, etc.
Development of the Hugli region:
- Several ports were opened by the colonisers – in the river port of Hugli. Britishers ultimately developed Kolkata as a leading centre of the country.
- Capital in 1773; Later, Kolkata was connected with interior parts by railway lines and road routes.
- Development of tea plantations in Assam and the northern hills of West Bengal, the processing of indigo earlier and jute later coupled with the opening of coalfields of the Damodar Valley and iron ore deposits of the Chotanagpur plateau, contributed to the industrial development of the region.
- The first Jute mill, the Rishra Jute Mill, opened in 1855. Cheap labour is available from thickly populated parts of Bihar, eastern Uttar Pradesh and Odisha.
- In 1947, the partition adversely affected the Cotton industry. The cotton textile industry also grew along with the jute industry, and paper, engineering, textile machinery, electrical, chemical, pharmaceuticals, fertiliser and petrochemical industries have also developed within this region.
- Factory of the Hindustan Motors Limited at Konnagar and the diesel engine factory at Chittaranjan are landmarks of this region.
- The location of the petroleum refinery at Haldia has facilitated the development of a variety of industries.
The industrial growth of this region has slowed down in comparison to other regions. The decline of the jute industry is one of the reasons.
Bangalore-Chennai Industrial Region:
It is the most rapidly developing industrial region.
- Development: Till 1960, industries were confined to Bangalore, Salem and Madurai districts but now they have spread over all the districts of Tamil Nadu except Viluppuram. Since this region is away from the coalfields, its development is dependent on the Pyakara Hydroelectric plant, built in 1932.
- The cotton textile industry was the first to take root due to the presence of cotton-growing areas. Along with cotton mills, the loom industry spread very rapidly.
- Several heavy engineering industries converged in Bangalore. Aircraft (HAL), machine tools, telephone (HTL) and Bharat Electronics are industrial landmarks of this region.
- Important industries are textiles, rail wagons, diesel engines, radio, light engineering goods, rubber goods, medicines, aluminium, sugar, cement, glass, paper, chemicals, film, cigarettes, matchboxes, leather goods, etc.
- Petroleum refinery at Chennai, iron and steel plant at Salem and fertiliser plants are recent developments.
Gujarat Industrial Region:
Nucleus between Ahmedabad and Vadodara but this region extends Uttar Pradesh to Valsad and Surat in the south and to Jamnagar in the west.
Important industrial centres of this region are Ahmedabad, Vadodara, Bharuch, Koyali, Anand, Khera, Surendranagar, Rajkot, Surat, Valsad and Jamnagar.
Development: location of the cotton textile industry since the 1860s. Grew as an important textile region with the decline of the cotton textile industry in Mumbai. Located in a cotton growing area, this region has the double advantage of the proximity of raw materials as well as of market.
- Discovery of oil fields led to the establishment of petrochemical industries around Ankleshwar, Vadodara and Jamnagar.
- Port at Kandla helped in the rapid growth of this region.
- Petroleum refinery at Koyali provided raw materials to a host of petrochemical industries.
The region has now diversified.
- Besides, textiles (cotton, silk and synthetic fabrics) and petrochemical industries, other industries are heavy and basic chemicals, motors, tractors, diesel engines, textile machinery, engineering, pharmaceuticals, dyes, pesticides, sugar, dairy products and food processing.
- Recently, the largest petroleum refinery has been set Uttar Pradesh at Jamnagar.
Chotanagpur Region:
It extends over Jharkhand, northern Orissa and western West Bengal and is known for its heavy metallurgical industries.
Important centres are Ranchi, Dhanbad, Chaibasa, Sindri, Hazaribag, Jamshedpur, Bokaro, Rourkela, Durgapur, Asansol and Dalmianagar.
Development:
With discovery of coal in the Damodar Valley and metallic and non-metallic minerals in Jharkhand and northern Orissa and other ores – facilitated the location of heavy industries in this region.
- Six large integrated iron and steel plants at Jamshedpur, Burnpur-Kulti, Durgapur, Bokaro and Rourkela are located within this region.
- Power requirement: thermal and hydroelectric plants have been constructed in the Damodar Valley.
- Densely populated surrounding regions provide cheap labour and the Hugli region provides a vast market for its industries.
- Heavy engineering, machine tools, fertilisers, cement, paper, locomotives and heavy electricals are some of the important industries in this region.
Vishakhapatnam-Guntur Region:
From Vishakhapatnam district to Kurnool and Prakasam districts in the south.
Important centres: VishakhapaTamil Naduam, Vijayawada, Vijaynagar, Rajahmundry, Guntur, Eluru and Kurnool.
Development:
Hinges upon Vishakhapatnam and MachilipaTamil Naduam ports and developed agriculture and rich reserves of minerals in their hinterlands.
- Coalfields of the Godavari basin provide energy.
- The shipbuilding industry was started at Vishakhapatnam in 1941.
- Petroleum refineries based on imported petroleum facilitated the growth of several petrochemical industries.
- Sugar, textile, jute, paper, fertiliser, cement, aluminium and light engineering are the principal industries of this region.
- One lead-zinc smelter is functioning in Guntur district.
- The iron and steel plant at Vishakhapatnam uses the Bailadila iron ore.
Gurgaon-Delhi-Meerut Region:
A fast growth in the recent past.
Other Centres: Gurgaon, Delhi, Shahdara, Faridabad, Meerut, Modinagar, Ghaziabad, Ambala, Agra and Mathura.
Development of the region:
- This region is located far away from the mineral and power resources, and therefore, the industries are light and market-oriented.
- Electronics, light engineering and electrical goods are major industries in this region. Besides, there are cotton, woollen and synthetic fabrics, hosiery, sugar, cement, machine tools, tractors, cycle, agricultural implements, chemical and vanaspati industries which have developed on a large scale. The software industry is a recent addition.
- To the south lies the Agra-Mathura industrial area which specialises in glass and leather goods. Mathura with an oil refinery is a petrochemical complex.
Kollam-Tiruvanantapuram Region:
It is spread over Thiruvananthapuram, Kollam, Alwaye, Ernakulam and Alappuzha districts.
Important industrial centres: Kollam, Tiruvanantapuram, Alluva, Kocchi, Alappuzha, and Punalur.
- Plantation agriculture and hydropower provide an industrial base to this region. Located far away from the mineral belt of the country, agricultural products processing and market-oriented light industries predominate the region.
- Among them, cotton textile, sugar, rubber, matchbox, glass, chemical fertiliser and fish-based industries are important.
- Food processing, paper, coconut coir products, aluminium and cement industries are also significant.
The location of the petroleum refinery at Kochi has added a vista of new industries to this region.
Related FAQs of Manufacturing Industries
India’s manufacturing sector contributes about 17% to the GDP, which is lower than the 25–35% seen in many East Asian countries. To boost economic growth and job creation, India aims to raise this to 25% in the coming decade.
Great question! Industrial location depends on raw materials, skilled labour, capital, power supply, and market access. Urban areas also attract industries because of “agglomeration economies” – where industries benefit by clustering together.
India is the world’s second-largest producer of steel, with major steel plants located near raw material sources like Chhattisgarh, Odisha, and Jharkhand. However, issues like costly coal imports and infrastructure gaps hinder its full potential.
Thanks to vast cotton farming areas, skilled labour, and high domestic demand (India is a tropical country!), the cotton industry thrives. Tamil Nadu, Gujarat, Maharashtra, and UP are key hubs, with both traditional handlooms and modern mills.
Jute, once booming, now faces challenges from synthetic alternatives but is gaining relevance as an eco-friendly material. Sugar, on the other hand, remains a key agro-industry, especially in Maharashtra and UP, but is heavily seasonal and water-dependent.